Table Of Content
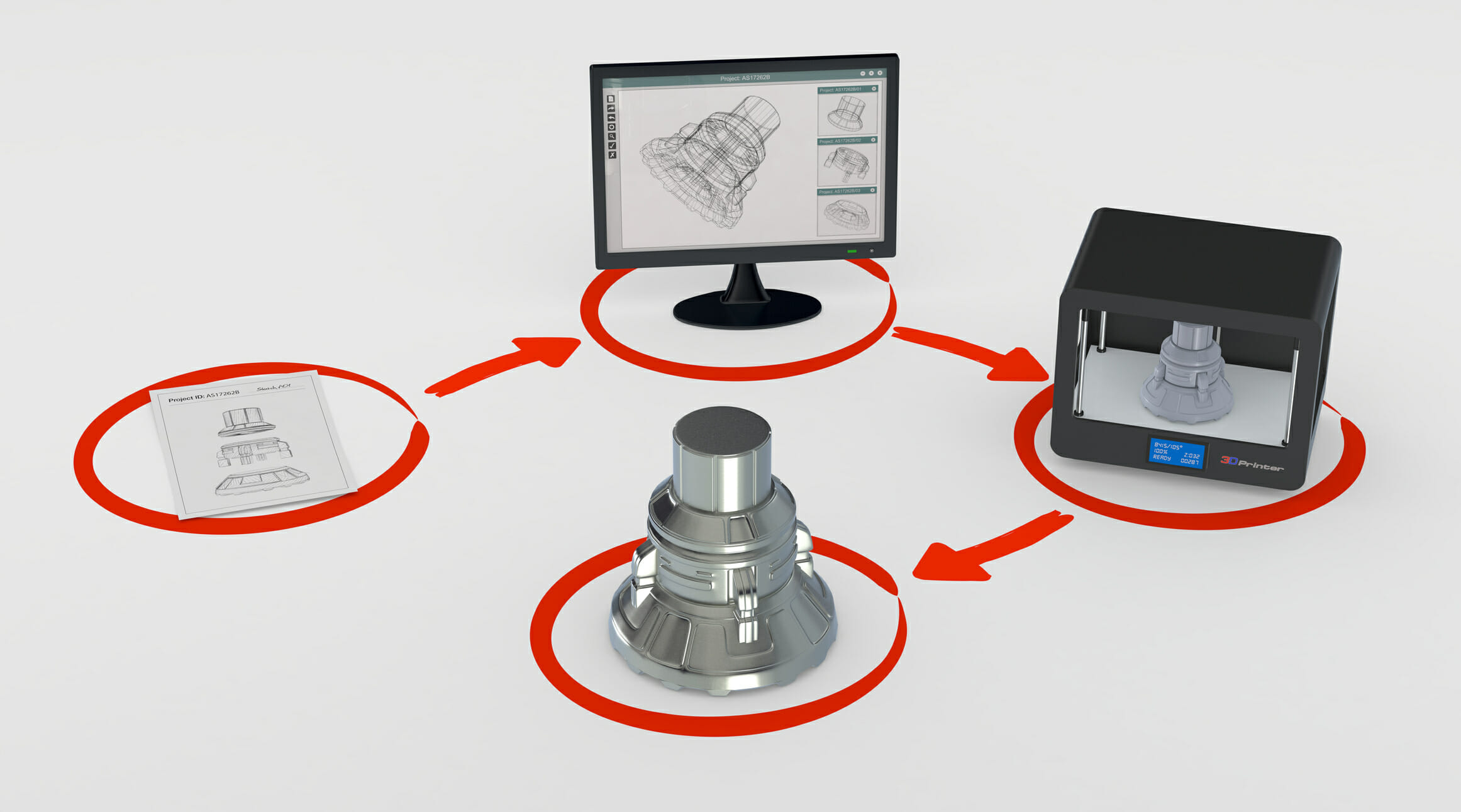
Everything in the electronics manufacturing process must be optimized—there is simply no time for multiple late-stage iterations or for costly mistakes that waste time and material. DFM is a critical to speeding up the process and minimizing costs by optimizing the handoff between design and manufacturing and ensuring first-time-right PCB production. Doing a DFM analysis before beginning the mold design process helped identify key areas that needed improvement. Engineers optimized the gear teeth' arrangement using DFM principles and purposefully reduced rib features to streamline the component design. This simplified manufacturing for the consumer while also reducing material use, cost and overall component weight.
Key Qualifications
As a result they were able to move the same volume of cargo with fewer vehicles, reducing emissions by 22 percent and increasing their efficiency by 10 percent. Designers can print multiple mold iterations at a fraction of the cost and time to produce machined tooling. Read on to learn about DFM rules and principles for common manufacturing methods and the various ways 3D printing is used in manufacturing. To generate in depth DFM insights, there is no substitute for detailed digital manufacturing simulation.
Manufacturing process
Ideally, DFM guidelines take into account the processes and capabilities of the manufacturing industry. While DFM is applicable to the design process, a similar concept called DFSS (design for Six Sigma) is also practiced in many organizations. Airbus is confident that a planned A350 production rate hike to 12 aircraft monthly can be accommodated both by the supply chain and the airframer’s own industrial system. Ever wonder exactly why materials like marble and terrazzo tile are so in right now? And now, the Brooklyn-based studio is partnering with In The Pursuit to spread its gilded stone look.
What Is the Benefit of Using Design for Manufacturing With 3D Printing?
Be sure to discuss the design with your contract manufacturer, who can ensure that your design conforms to good manufacturing principles for the selected process. There are numerous designs for manufacturing examples in industrial environments that can help us develop a better understanding of how it works in a practical environment. This section will go over a few of these to try to give you a flavor of design for manufacturability in practice. The solutions can include dimensional changes like extra wall thickness to accommodate mechanical loads. They may suggest a different material due to its better thermal stability. In other cases, a specific surface coating may be added to the manufacturing process to protect the part against chemical exposure.

This allows for quicker time-to-market, lower costs and better product quality. It's crucial to involve manufacturing teams from the early stages of the design process. This ensures that the design is feasible and cost-effective from a manufacturing perspective. Early collaboration between design and manufacturing teams can help identify potential manufacturing issues and allow for design modifications before the production phase. Design for manufacturing (DFM) is the process of efficiently engineering or designing a product, usually in the product design phase, to lower production costs.
Design for Manufacturability (DFM) for Early-Stage Companies - Design News
Design for Manufacturability (DFM) for Early-Stage Companies.
Posted: Mon, 23 Oct 2023 07:00:00 GMT [source]
Need Top Engineering Expertise?
This reduces production workload, focuses manufacturing effort on non-standardized parts, and reduces costs. The number of components in a mechanical assembly can be minimized for simplicity, cost reduction, and less waste. While this may not always be possible, DFM analysis always focuses on identifying and eliminating redundant parts through careful analysis. Design for manufacturing, or DFM as it is commonly abbreviated, is a core engineering concept that involves all activities that focus on making an idea into a practical, operational product.
To join the conversation, and become an exclusive member of IndustryWeek, create an account today!
Decreasing the number of parts in a product is the quickest method to save costs since you are reducing the quantity of material necessary and the amount of engineering, manufacturing, labor, and shipping expenses. Design for Manufacture and Assembly consists of two primary methodologies. DFM and DFA aim to optimise design while lowering labour, materials, and overhead costs. The book Computer-Aided Manufacturing offers 10 generally accepted Design for Manufacturing principles that were developed to help designers decrease the cost of and complexity of manufacturing a product.
A platform for growth: DfMA and virtual prototyping for Everton Stadium - Buro Happold
A platform for growth: DfMA and virtual prototyping for Everton Stadium.
Posted: Wed, 24 Apr 2024 16:39:54 GMT [source]
Design for Manufacturing vs. Design for Assembly
In particular, processes like surface-mount technology (SMT) and soldering are becoming more automated, generally lowering costs over the long term. DFMA applies these techniques to a company’s standard production line to create a product that is easy to manufacture and assemble. It may use integrated product development disciplines such as concurrent engineering to bring down costs and improve product reliability. As most of the design and manufacturing issues are addressed in the early stages of the design process, fewer issues crop up during the actual manufacturing process.
OUTCOMES OF AN EFFECTIVE DFM
Choosing an expensive and hard-to-manufacture metal will be over-engineering. Similarly, if it is meant to protect an expensive, high-quality item against shock loads, composites might be the go-to choice. Engineering design is an iterative process and it is expected to experience some back and forth between design and production. In rare cases, major design changes might be suggested to the design engineering team, which then requires collaborative work between both teams to come up with the best solution.
One of the most significant obstacles to DFM implementation is resistance to change. Implementing DFM requires a shift in mindset from designing products based solely on form and function to designing products with manufacturing in mind. This can be a significant change for design teams, who may be used to working independently of manufacturing teams. There are various software and tools available that can aid in DFM analysis. These tools can evaluate a design's manufacturability, identify potential manufacturing issues, and suggest design improvements.
Using DFM analysis tools can help identify potential manufacturing issues early in the design phase, allowing for timely design modifications. This can significantly reduce production costs and lead times, as well as improve product quality and reliability. Design for manufacturability (also sometimes known as design for manufacturing or DFM) is the general engineering practice of designing products in such a way that they are easy to manufacture. The concept exists in almost all engineering disciplines, but the implementation differs widely depending on the manufacturing technology. DFM describes the process of designing or engineering a product in order to facilitate the manufacturing process in order to reduce its manufacturing costs.
This backlog is set to rise with Indian carrier IndiGo’s confirmation that it will take 30 A350s. Airbus has been gradually recovering A350 production, aiming to restore the 10-per-month figure in 2026. Now more than ever, students across engineering disciplines are seizing opportunities in manufacturing related careers.
Bar stock is generally close to 1/2 of the cost of plate on a per pound basis. So although the material form isn't directly related to the geometry of the component, cost can be removed at the design stage by specifying the least expensive form of the material. And while Floyd is already a fairly large business, many smaller furniture makers such as Kin & Company build everything in-house. "It enables us to approach product development from a more integrated perspective, with the creative and craft processes informing one another," explains Kira de Paola, a co-founder of the studio. For example, air freight may be the most time-efficient transport in the supply chain, but it has a high cost and high environmental impact.
3D printed surrogate parts can be used to replace expensive parts or parts that are not readily available, savings weeks or months in production. Additionally, an interesting way to get a peek into design choices (and mistakes) made by other companies is reading or watching product teardowns. Some of the world’s most innovative and sustainable manufacturers use aPriori, including Boeing, Carrier, Danfoss, Navistar, Thales, and Toyota.
In response, companies began to adopt a more systematic approach to product design, incorporating consideration of production processes, tooling, and other manufacturing factors into the design process. Over time, this approach evolved into the modern concept of DFM, which is now widely used in the manufacturing industry to optimize product design for efficiency and cost-effectiveness. Design for Manufacturing refers to the practice of designing products in a way that optimizes their manufacturability. The primary goal is to minimize production costs, reduce complexity, and ensure product reliability while adhering to quality standards.
No comments:
Post a Comment