Table Of Content

But this isn't to say that Floyd's business model is limited to a singular item. The company, which operates out of Detroit, Michigan, also sells sleek tables and table legs. Below, from Kalon to Amigo Modern and beyond, 16 of our favorite furniture designers of the moment who manufacture in the U.S.—in honor of the Fourth of July. Trine, like so many of his peers, isn't only incentivized by his bottom line. "He worked for companies that manufactured overseas, and he would be gone for two to four weeks at a time. Now that I have two young daughters, I want to be home as much as possible."
DFMA related products
In the medical device industry, DFM is all about making surfaces that are smooth and simple to clean. This ensures the devices are in accordance with regulations and that patients are safe. In automotive engineering, the goal of DFM is to save maintenance time and expenses by making engine parts that are easy to access and replace. Aerospace DFM solutions aim to improve fuel economy and performance by creating lighter and less complex aircraft components. Material selection is a critical aspect of product design, as it directly influences the performance, cost, and sustainability of the final product. Ensuring that the product is reliable and durable is another critical aspect of DFM.
Build Your DFM Process with DISHER
It is important to evaluate how preferring one raw material form over another affects the grand scheme of things. These tools enable deep DFM modeling and real-world testing at a fraction of the original cost. Thus, an increasing number of manufacturers are integrating DFM into their organizations to reap its many benefits. The most easily machined types of metals include aluminum, brass, and softer metals. As materials get harder, denser and stronger, such as steel, stainless steel, titanium, and exotic alloys, they become much harder to machine and take much longer, thus being less manufacturable. Most types of plastic are easy to machine, although additions of fiberglass or carbon fiber can reduce the machinability.
History of Design for Manufacturability
When manufacturing experts collaborate with designers, they may detect waste in manufacturing and provide more efficient and sustainable options. The availability and capabilities of the manufacturing technology can impact the production process’s cost and efficiency. And remember that unless it must be trade show grade, choose function over flashy for your surface finish. The duration of a design for manufacturing (DFM) process varies based on the complexity of the product and the manufacturing needs.
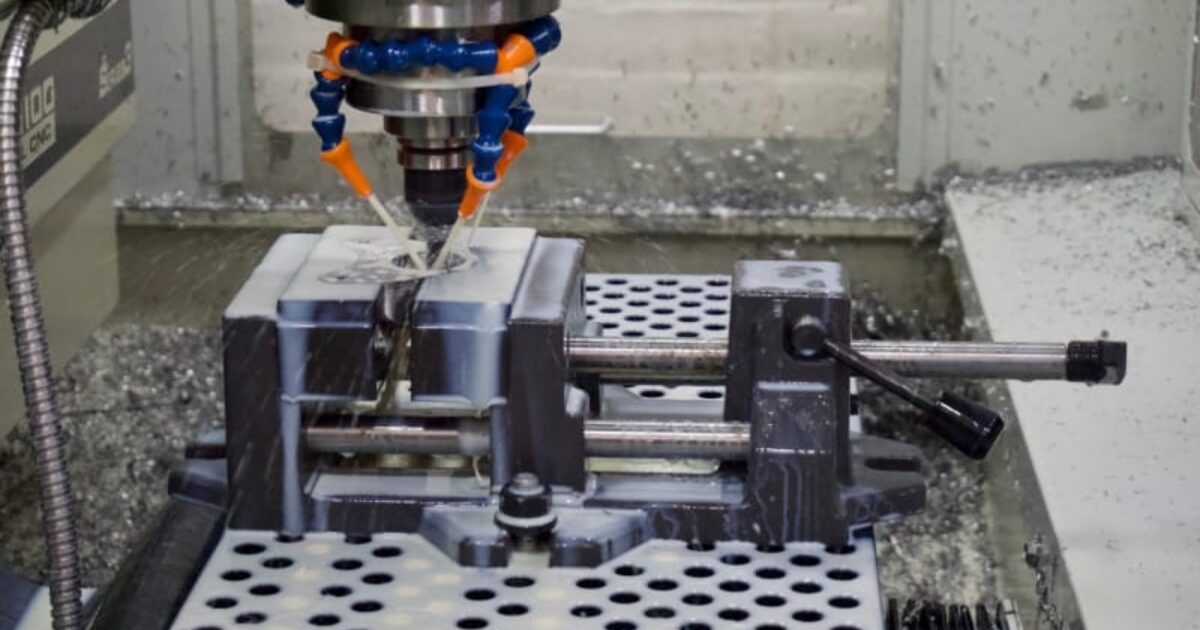
Finite Element Analysis (FEA) is a powerful method for optimizing materials and reducing weight; this method assesses how designs will react under various loads and circumstances. Organizations can also promote DFM principles by cultivating a feedback loop culture and a culture of continuous development. Regular design reviews should include soliciting feedback from manufacturing teams and learning from previous design stages.

Consequently, this also opens up new avenues for market expansion and company growth. DFM ensures the financial viability of the product development process and guarantees healthy returns on investment. Designing engine components that are easy to access and replace, reduces maintenance time and costs. Using standardized fasteners and connectors to simplify assembly and reduce the need for custom parts. From test-point definition and validation to DFM analysis during layout, designers can eliminate errors before PCB assembly. DFM validation ensures a seamless and error free design-to-manufacturing hand-off.
Five Digital Threads Unify And Simplify Electronic Systems Design And Manufacturing - SemiEngineering
Five Digital Threads Unify And Simplify Electronic Systems Design And Manufacturing.
Posted: Thu, 25 Jan 2024 08:00:00 GMT [source]
Assembly →
The methodologies used in DFM often involve cross-functional teams that work together from the initial stages of product design. This ensures that all aspects of manufacturability are considered early in the design process. Testing all aspects of a PCB design isn’t practical, so engineers must develop methods of making testing during design easier and less expensive. This process aims to detect design defects with minimal impact on the assembly and packaging phases.
As technology and production processes continued to evolve, the principles of DFM have adapted and expanded to include new considerations such as automation, material selection, and sustainability. Today, DFM is widely recognized as a critical component of a successful manufacturing strategy and is used by manufacturers of all sizes and across all industries. The principles of DFM are integrated into modern product design software and tools and are taught as part of engineering curriculums. The use of DFM has led to significant improvements in production efficiency, reduced production costs, and increased product quality, making it an essential component of any successful manufacturing strategy. Additionally, DFM sets quality standards for manufacturability such as raw material and components consistency, an efficient assembly process, and reducing the number of parts.
The conceptual design may not always be capable of withstanding such environmental conditions. Therefore, DFM engineers apply design for manufacturing principles to sort out such problems. During DFM analysis, engineers identify all such issues and come up with solutions for them. In most cases, it is limited to small tweaks in the design here and there. For example, in DFM for CNC machining, the suggestions can include adding fillets to sharp internal corners (see figure below) to accommodate cutting tool radius.
It is important to distinguish between realistic and unrealistic expectations to reduce manufacturing costs. A product that will be used only in dry areas over its lifetime does not need marine-grade specifications. During DFM, we only consider normal operating conditions to eliminate unnecessary manufacturing costs. Take the example of a plastic product designed with different wall thicknesses.
Designing aircraft components with tight tolerances to ensure precision and reliability.Using materials that are lightweight yet strong, such as carbon fiber composites, to reduce fuel consumption. Using modular components that can be easily assembled and disassembled, reducing shipping and storage costs.Designing furniture with fewer complex joints and fasteners for more efficient production. Once upon a time was a manufacturer who refused to apply Design for Manufacturability (DFM). The company crafted intricate metal sculptures for commercial use, but their unwillingness to simplify designs resulted in long production times and costly delays. This will reduce the cost of new designs while improving inventory management and time-to-market. To maximize DFM results and strike the right balance between design needs and production limitations, engineers must take these tradeoffs into account.
While carrying out DFM, manufacturing engineers must always keep testing and compliance requirements at the back of their minds to prevent any hiccups in later stages. A product that can be manufactured at a fraction of the original cost but cannot pass certifications will never reach the market. A significant contributing factor to the cost of a machined component is the geometric tolerance to which the features must be made. The tighter the tolerance required, the more expensive the component will be to machine.
Effective communication and collaboration between design and manufacturing teams are crucial for successful product development. By working together, designers and manufacturing teams can identify potential manufacturing issues early in the design process, reducing the likelihood of costly redesigns later on. Thus, designing products using DFM creates a solid plan for product development before the design process even begins.
For example, 3D printing may enable one monolithic part design instead of manufacturing multiple components. Additionally, when a design is reviewed at an early stage, it can also be optimized for specific production volumes, including high mix, low volume production. Given the complexity of the electronic manufacturing process, DFM principles are applied in specific ways to several key stages within the PCB design-to-manufacturing workflow, and even beyond it. This has given rise to several subsets of DFM, each of which focuses on optimizing different aspects of the manufacturing process. The capacity to generate intricate textures, patterns and geometries is only one of the many design freedoms made possible by additive manufacturing. AM can merge dozens of separate components into one or condense assembly into one, like two sides of a hollow item.
Simulation benefits customers, equipment suppliers, and supply chain partners. It also lessens the hassle and cost of the old-fashioned trial and error method, which can lead to unnecessary rearranging of machinery on a production line throughout the manufacturing operations. Designers can optimize designs proactively by evaluating moldability, assembly feasibility and material selection when using state-of-the-art design and simulation tools.
No comments:
Post a Comment